At MiroTech, we provide high-quality PCB test fixture kits that offer flexibility, precision, and affordability for all your PCB testing needs. Our kits include a range of mechanical options—such as clamshell test fixture kits and non-wiping linear collapse test fixture kits—to suit different testing scenarios and budgets. These customizable kits empower users to cut their own test plates, ensuring optimal accuracy for detecting PCB soldering defects and other functional testing requirements.
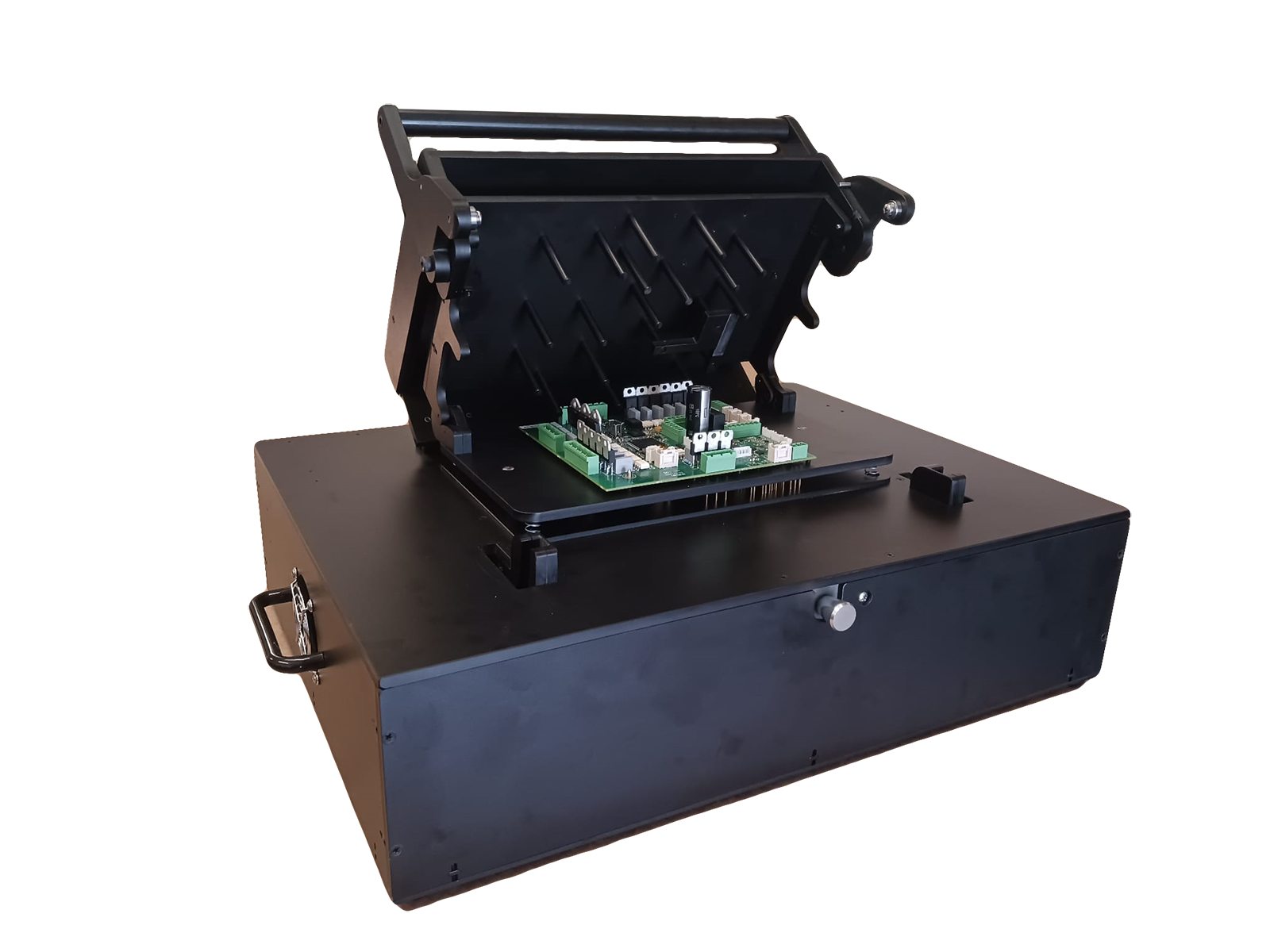
Mirotech PCB Test Fixture Kits: A Superior Alternative to Traditional Mechanical Presses
While traditional mechanical presses have been a staple in PCB testing, Mirotech’s fixture kits offer an affordable and flexible alternative. With clamshell test fixture kits for fast engagement and non-wiping linear collapse test fixture kits for sensitive testing requirements, we provide solutions for any testing scenario. Our kits are ideal for testing UUT (unit under test) devices, allowing users to create customized setups with the ability to cut their own test plates. Whether you’re using a bed of nails setup or another fixture configuration, our kits adapt to meet your specific testing needs, including the detection of PCB soldering defects and other performance issues.
Manufacturing and programming such fixtures typically take four to six weeks.
Applications of MiroTech Fixture Kits
Mirotech’s PCB fixture kits are perfect for a wide variety of testing applications, including:
- Functional Testing: Ensure your PCB meets all operational specifications by performing thorough tests with our customizable fixture kits.
- Detection of PCB Soldering Defects: Customize your test plates to effectively identify PCB soldering defects, ensuring that your PCBs meet quality standards.
- Prototyping: Test your PCB prototypes quickly and efficiently, allowing you to move through the development cycle faster.
- Production Line Testing: Our fixture kits, including the clamshell test fixture kits, are designed to handle high-volume testing with minimal downtime, perfect for production environments.
Mirotech manufactures PCB Test fixtures kits in the Greater Toronto Area, providing high-quality solutions for efficient and accurate PCB testing.
Your UUT is in safe hands, mechanically
The non-wiping mechanism involves a controlled, uniform, and consistent vertical movement during PCB testing. This ensures that all test points on the PCB are contacted simultaneously and with equal force by the test probes or pogo pins. This uniform contact is critical for the following reasons:
Consistent Test Results: By ensuring that each test point receives the same amount of pressure, the non-wiping mechanism contributes to the accuracy and repeatability of test results. This is crucial for identifying faults and verifying the functionality of the UUT.
Minimizing Wear and Tear: A key feature of the non-wiping action is that the test probes make contact with the test points without sliding across them. This reduces wear and tear on both the probes and the PCB, minimizing the risk of damage. As a result, the lifespan of the test fixture and the UUT is extended, reducing the frequency of replacements and repairs.
Enhanced Reliability: The linear collapse design, which incorporates the non-wiping mechanism, ensures precise alignment and reliable connections during testing. This mechanism maintains the integrity of the contact points, contributing to the overall reliability of the testing process.
Protection of Test Components: By avoiding lateral movement or sliding, the non-wiping mechanism protects sensitive components on the PCB. This is particularly important for high-density boards where test points are closely spaced, and any sliding action could cause shorts or other damage.
In summary, the non-wiping mechanism in UUT test fixture design is essential for maintaining the reliability, precision, and efficiency of the testing process. It ensures high-quality results while protecting both the test fixture and the unit under test, ultimately contributing to more robust and reliable electronic products. Whether using a bed of nails or flying probe testing, the principles of controlled, precise contact are critical for achieving accurate and repeatable test results.
Let’s work together on your
next project
We have been providing our customers with test fixtures for over 20 years. We have a proven track record of providing excellent customer service, quality products, and reasonable prices.